CO2 electrification
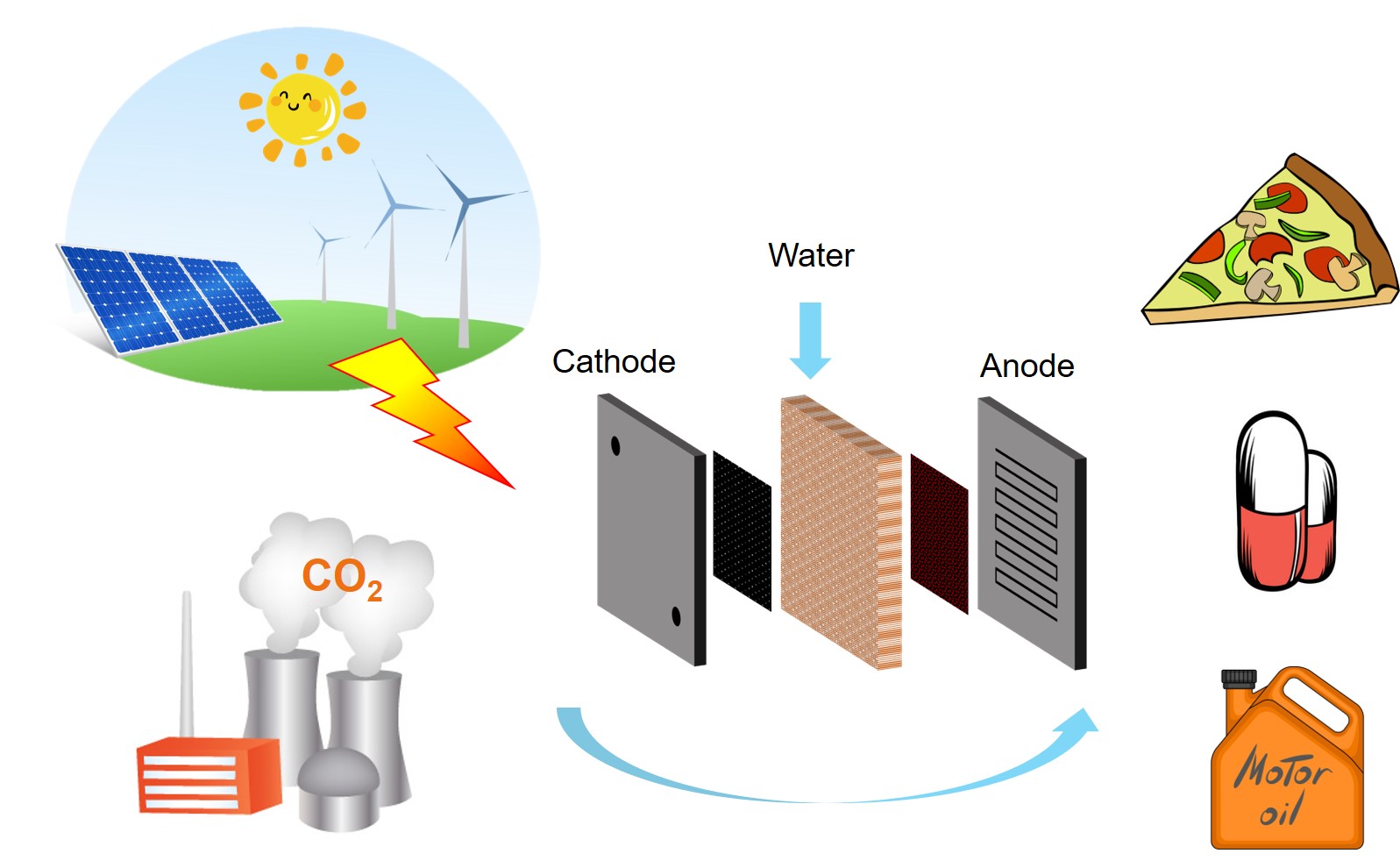
In the global context where carbon neutralization is strongly advocated, the use of CO2, water, and renewable energy as direct feedstock for the synthesis of value-added products is a revolutionary route of breaking the traditional energy structure which relies on fossil fuels. Electrochemical CO2 reduction in particular has been championed as a promising technology aiding in the energy transition and decarbonization. Our prime interest is to develop transformative technologies, based on electrochemical CO2 reduction, to realize the practical production of chemicals, fuels, drugs and even foods.
Our current work focused on the exploration of highly efficient catalysts as well as the design of novel reactors for electrochemical CO2 reduction. The reaction mechanism is also what we devote to exploring, aiming at providing insights and guideline for catalyst design. Furthermore, our efforts will be directed towards scaling up of CO2 electroreduction for practical applications, bridging the gap between fundamental study and entity industry.
So far our group have developed a series of controllable synthesis methods to precisely tune the structural characteristics of catalysts, such as composition, crystal plane, size, defects, surface, interface, as well as coordination environment. We have successfully synthesized defect-abundant materials, 2D-materials, single atom-carbon materials, single atom alloys, high entropy alloys, and so on. For the part of cell design, we have developed a novel solid-electrolyte reactor to realize the direct production and collection of pure liquid products, exempting from the downstream treatment such as products separation and purification.
By virtue of solid foundation and technical reserves, Chuan’s group have done a lot of excellent work on electrochemical CO2 reduction. Our group have introduced single-atom alloy catalyst that can exclusively (~96% Faradaic efficiency) convert CO2 to formate with unprecedented activity over 1 ampere per square centimeter. By integrating the catalysts with solid-electrolyte reactor, we showcase a continuous production of pure formic acid solution at 100 milliamperes per square centimeter over 180 hours. We also demonstrated a direct production of pure acetic acid with partial current density ramped up to 420 mA cm-2. One step further, our group concentrate on how to further upgrade the C1/C2/C3 products such as formic acid, acetic acid and proponal to senior products like glucose.